Research and development
The Cooling of generators by using hollow conductors in the wind energy
For several years now, we have been investigating the use and efficiency of hollow conductors for the active cooling of a generator. The hollow conductors were tested with various cooling media. Beside the theoretical preliminary work, the feasibility and the operating characteristics were experimentally confirmed on a specially developed test rig. In the patent EP000001852956, we applied for property rights regarding the use of hollow conductors in gearless wind energy generators.
Reduction of tower head masses by integral construction and use of lightweight materials
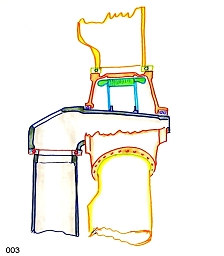
The reduction of the tower head mass has always been an important topic, because it is responsible for a great part of the structure costs. Apart from the usual methods to reduce masses for the generator and the structure, we do research aimed at increasing the percentage of lightweight construction material in wind turbines. In contrast to most wind turbines which dominate the market, including both turbines with gearboxes and those with direct drive, we developed a way to increase the amount of lightweight construction material. In our designs, the generator and rotor hub are constructed as a single part. This construction method was partially used in the project
NEW82.
In our new research projects the usability of lightweight materials will be
examined more closely. Due to the large number of units, a lot of construction
parts are now made of cast material. The most commonly used materials are nodular graphite castings with steel-like densities and unwelcome manufacturing restrictions, for example the necessary minimum wall thicknesses are within the centimetre range, which may considerably restrict a possible lightweight design. By using low-density materials, with lower manufacturing restrictions and high strength, there is a real potential to reduce the tower head mass.
Specialized solutions for series production
Due to the dimensions of gearless wind turbines and due to the fact that the manufacturers’ drive train designs vary considerably, it is necessary to design specialized manufacturing and mounting tools, an area in which we have profound experience. This may be very useful, especially when the wind turbine design and the manufacturing tools are realized at nearly the same time and require prompt and optimal incorporation into the series production process.
Alternative solutions for blade pitch controls
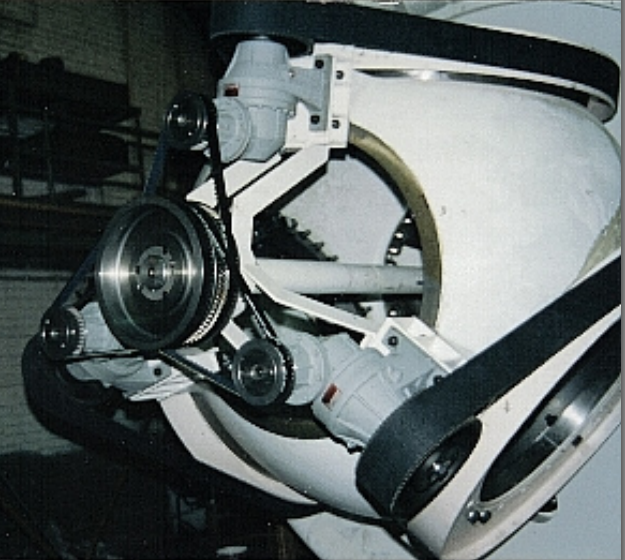
Pitch control is one of the most important systems of a modern wind turbine, and it requires considerable maintenance. Besides determining economic success by optimal positioning of the rotor blades in the wind direction, it is also responsible for power control, stopping and taking a resting position without risk. That is why INNOWIND took up this subject early and developed a pitch control system with a drive belt, wich is also used in VENSYS turbines.
The recent studies favour a centralized pitch control, which allows a fail-safe function and a construction without a slip ring which is almost maintenance-free.
Alternative solutions for the yaw control
Regarding yaw control, systems with a high demand for maintenance are still the state of the art. For this reason, we do research and development works in the field of azimuth propulsion in order to find an alternative solution. This approach operates without a four-point-bearing with the help of a hydraulic fixation. We expect considerable improvements with regard to a lower maintenance and a simplified architectural system, which is economically more advantageous.
Automated assembly procedure for stator iron core
The iron core of an electrical machine consists of many layers of coated electrical sheets. These thin layers minimize the losses due to eddy currents. For handling reasons the sheets are segmented what leads to a high workload of more than 100 working hours to produce one iron core.
In 2010 INNOWIND developed an automated stacking device for big stator iron packets. The machine produces iron cores by stacking, aligning and pressing sheet ring segments automatically.
Concept for the electrical and mechanical testing of wind turbine
Wind turbines need to endure around 10e9 load cycles throughout their whole lifetime. Therefore a prediction of their fatigue strength is essential. Solely numerical simulations cannot fulfil this requirement and so physical fatigue testing is needed. Existing test rigs are very expensive since hydraulic actors are used to introduce high frequency aerodynamic loads.
INNOWIND developed a concept that needs nearly no hydraulic power for applying the loads and can test the electrical as well as the mechanical system simultaneously.
Feasibility study for a multi-rotor wind turbine
Many manufacturers work on huge prototypes for bigger than current wind turbines. INNOWIND questions this continuous growth of single turbines. Based on theoretical principles it is shown that upscaling of turbines results in higher masses per MW and thus higher specific costs. Therefore we propose a multi turbine what is a wind plant with several rotors attached to one single tower. This approach seems to be economically more promising than further growth in turbine size.